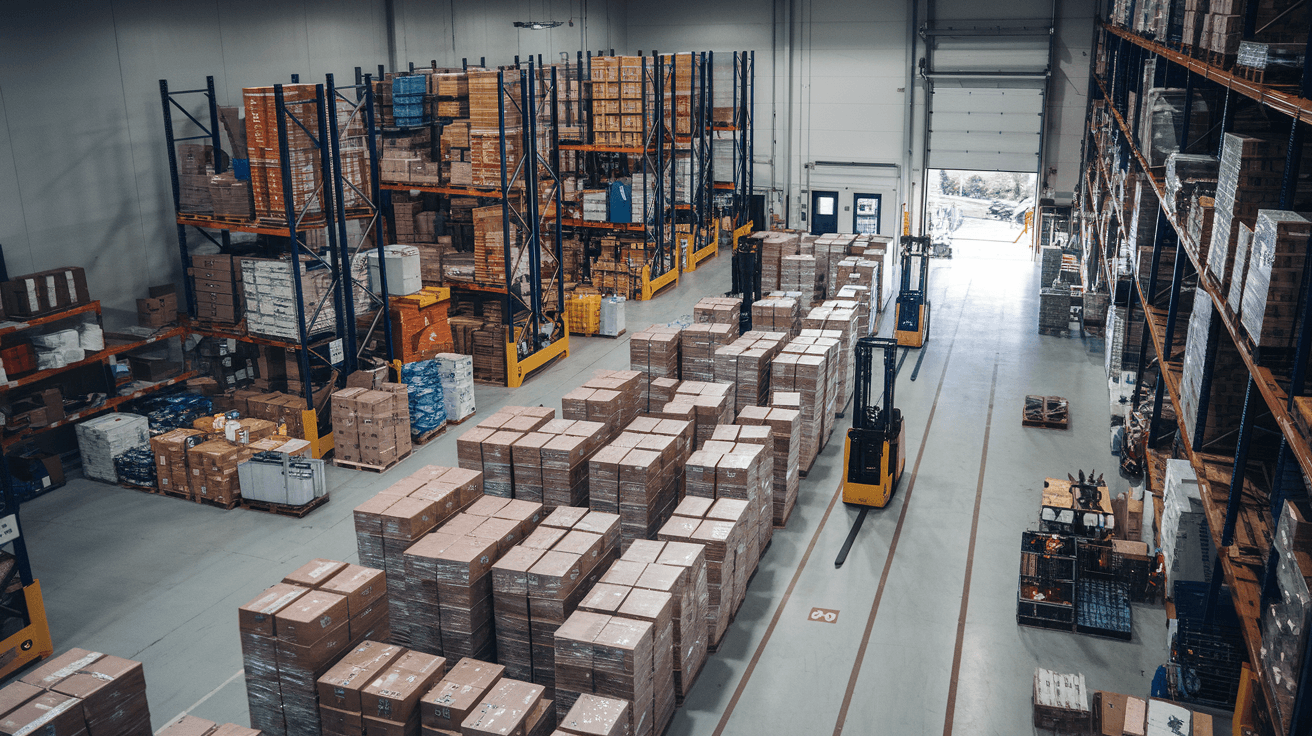
Warehouse Inventory Management | The Comprehensive Guide
22 April, 2025
By xavier
Share to
Warehouse inventory management (WIM) is the process of overseeing the flow of goods in and out of a warehouse. It ensures that the right products are available at the right time, in a world where speed and efficiency matter, WIM plays a crucial role.
The evolution of WIM has been significant. It started as a manual process. Workers would count items by hand, often leading to errors. Then came digital systems. These made tracking easier. Now, we have automated systems that use technology to manage inventory. Think of it like moving from a typewriter to a computer. It’s faster and more accurate.
Today, WIM is more important than ever. Modern supply chains rely on it to keep things running smoothly. With the rise of e-commerce, businesses need to deliver products quickly. Effective WIM helps meet customer expectations. It reduces costs and improves efficiency. In short, strong inventory management is key to success in today’s market.
What is Warehouse Inventory Management?
Warehouse Inventory Management (WIM) is the process of overseeing and controlling the storage and movement of goods within a warehouse. It involves not only tracking inventory levels but also managing orders, monitoring sales, and coordinating deliveries. As a result, WIM plays a crucial role in the overall efficiency of logistics and supply chain operations. Businesses can meet customer demands more effectively by ensuring that the right products are in the right place at the right time. Ultimately, this can mean the difference between a satisfied customer and a missed opportunity or lost sale.
The key objectives of WIM include:
- Accuracy: Keeping track of what is in stock is vital. Mistakes can lead to overstock or stockouts.
- Efficiency: Streamlining processes in the warehouse helps save time and effort. Think of it like organizing your closet. The better you organize, the easier it is to find what you need.
- Cost Control: Managing inventory wisely can reduce costs. Avoiding excess stock means less money tied up in products.
- Customer Satisfaction: When orders are fulfilled accurately and quickly, customers are happy. Happy customers are more likely to return.
In short, effective warehouse inventory management is essential for smooth operations and success in the supply
Why Warehouse Inventory Management Matters
Effective warehouse inventory management is crucial for any business. Why? It directly impacts efficiency and profitability. When inventory is managed well, operations run smoothly. This means faster order fulfillment and happier customers.
On the flip side, poor inventory management can be costly. According to the US Department of Commerce, businesses can lose 11% of their annual revenues due to stockouts and overstocking. Think about that. If a product is out of stock, customers may turn to competitors. That’s lost sales. And overstocking? It ties up cash and increases storage costs.
But there’s good news. Effective inventory management systems can transform your operations. By using the right tools, businesses can:
- Reduce labor costs by up to 30%
- Boost order accuracy to over 99%
These benefits mean fewer mistakes and more satisfied customers. In the competitive market, every little improvement counts. Better inventory management leads to better overall performance
Types of Inventory in Warehouses
Raw Materials
Raw materials are the essential components used to create finished products—think of them as the fundamental building blocks of production. For example, a furniture maker relies on materials like wood, nails, and glue to craft their pieces. Therefore, managing raw materials effectively means keeping a close eye on both current inventory levels and future supply needs. By doing so, businesses can avoid production delays, minimize waste, and ensure a steady workflow.
Work-in-Progress (WIP)
WIP refers to items that are in the process of being made but aren’t finished yet. Imagine a car on an assembly line. It’s not just a frame; it’s a car that’s still getting worked on. Keeping tabs on WIP helps prevent delays and ensures smooth operations.
Finished Goods
Finished goods are the end products ready for sale. These are items that customers can buy. For example, a completed chair in a store. Knowing how many finished goods are on hand helps in planning sales and reorders.
Maintenance, Repair, and Operations (MRO) Supplies
MRO supplies are materials needed for maintenance and repairs. These items keep a warehouse running smoothly. Think of tools and cleaning supplies. They might not be sold but are crucial for daily operations.
Packaging Materials
Packaging materials are used to protect products during shipping and handling. This includes boxes, bubble wrap, and tape. Proper management of these materials ensures that products arrive safely and in good condition.
How Inventory Types Influence Management Practices
Each type of inventory affects how a warehouse is managed. For example:
- Raw materials require careful tracking to avoid production stops.
- WIP needs regular updates to meet delivery deadlines.
- Finished goods management focuses on sales forecasting.
- MRO supplies must be available to avoid downtime.
- Packaging materials are vital for protecting products.
Understanding these types helps in creating efficient inventory systems.
Core Warehouse Inventory Management Processes
Receiving and Inspecting Inventory
When new inventory arrives, it’s crucial to check its quality. This means inspecting items for damage and ensuring they match the order.
Documentation is important too. Every item should be logged properly. Once everything checks out, it’s time for put-away. This is where items are placed in their designated spots in the warehouse.
Storing Inventory
Storage is about more than just putting items on shelves. It involves:
- Slotting: Figuring out the best location for each item based on size and demand.
- Organization: Keeping everything tidy. This makes finding items easier.
- Accessibility: Ensuring items are easy to reach. If something’s hard to get, it slows down operations.
Picking and Packing
Picking is the process of gathering items for orders. There are different methods to do this:
- Batch picking: Collecting several orders at once.
- Wave picking: Picking items in waves based on shipping schedules.
- Zone picking: Each worker picks items from their assigned zone.
To reduce errors, techniques like automation can help. Automation enables faster, more accurate picking (Infor). This means fewer mistakes and quicker order fulfillment.
Shipping and Dispatch
Before items leave the warehouse, packing verification is key. Every item must match the shipment details. This helps avoid mistakes.
Shipment tracking is also important. It allows customers to see where their orders are at all times.
Replenishment and Returns
Replenishment is key to maintaining steady inventory levels. Through continuous stock review, businesses can ensure that high-demand items remain readily available, preventing stockouts and missed sales. Equally important is returns processing, which plays a vital role in overall inventory management. By making the return process smooth and hassle-free, companies not only recover valuable inventory but also strengthen customer satisfaction and loyalty.
Inventory Management Methods and Strategies
Just-in-Time (JIT)
Just-in-Time is all about timing. You get your stock just when you need it. No more, no less. This method helps reduce waste. It saves on storage costs too. Think of it as a quick dinner service. You only cook what you need when customers order.
ABC Analysis
ABC Analysis sorts your inventory into three categories.
- A items are the most valuable. They need close monitoring.
- B items are moderate in value. They require regular checks.
- C items are the least valuable. You can manage these with less effort.
This method helps focus your attention where it matters most.
FIFO (First-In, First-Out)
FIFO means you sell the oldest items first. This method is great for perishable goods. You avoid waste by ensuring items don’t expire. It’s like using the milk in the back of the fridge first.
LIFO (Last-In, First-Out)
LIFO works in the opposite way. You sell the newest items first. This can help with pricing during inflation. But, it’s not ideal for perishable items. Think of it as pulling the last toy off the shelf first.
FEFO (First-Expired, First-Out)
FEFO focuses on expiration dates. You sell items that will expire first. This method is crucial for food and medicines. It ensures you don’t lose money on expired stock. Imagine rotating your pantry items to use the oldest first.
Cycle Counting
Cycle counting involves counting a portion of inventory regularly. It’s not as daunting as a full inventory count. You can catch errors sooner. This method keeps your records accurate. Think of it like checking your bank account regularly to avoid surprises.
Choosing the Right Method for Your Business
Not every method suits every business. Consider your products, market, and goals. Each method has its pros and cons. Evaluate what fits best. The right choice can save you money and time.
Tools and Technologies for Better Inventory Management
Inventory Management Software/Warehouse Management Systems (WMS)
Inventory management software is crucial. It helps track inventory levels, orders, and deliveries. The market is growing fast, at a 16.1% CAGR. Why? There’s a high demand for real-time tracking. With the right WMS, businesses can:
- Improve accuracy
- Speed up processes
- Enhance customer satisfaction
Barcoding and RFID
Barcoding and RFID are game-changers for tracking inventory. They provide real-time updates. This means fewer errors. According to the WERC DC Measures Report, advanced systems achieve 99.3% inventory accuracy. That’s impressive.
Automated Alerts and IoT Sensors
Automated alerts and IoT sensors help manage inventory proactively. They notify you about low stock or potential issues. This leads to better loss prevention. You can catch problems before they escalate.
Mobile Devices and Cloud Integration
Mobile devices and cloud integration allow for on-the-go access. You can manage inventory remotely. This flexibility is essential in today’s fast-paced world. You’re not tied to your desk. You can make decisions from anywhere.
Robotics and Automated Storage/Retrieval Systems
Robotics and automated systems can transform your warehouse. They reduce labor needs and speed up operations. Plus, they minimize errors. According to Infor, automation can cut stock holding costs by 20%. That’s significant savings.
Best Practices for Warehouse Inventory Management
-
Organize warehouse layout for optimal flow. Think about how products move. Place items that are often picked together close to each other. This saves time and speeds up order fulfillment.
-
Implement logical inventory categorization. Group similar items together. Use a simple system, like categories or colors. This makes finding items quick and easy.
-
Use technology for real-time tracking. Tools like barcode scanners help keep track of products. You’ll know where everything is at any moment. No more lost items.
-
Conduct regular inventory audits and cycle counts. Schedule these often. This helps catch mistakes early. It also keeps your inventory accurate.
-
Automate processes where possible. Use software to manage orders. This cuts down on manual work. Less work means fewer mistakes.
-
Train staff effectively and foster accountability. Make sure everyone knows their roles. Training reduces errors. When staff feels responsible, they work better.
-
Reduce human error through checklists and technology. Checklists are simple but effective. They ensure every task is completed. Tech tools can also alert you to potential mistakes.
-
Continuously review and optimize inventory levels. Regularly assess what you have. Adjust stock based on demand. This keeps your inventory lean and efficient.
Key Performance Indicators (KPIs) and Metrics
When it comes to warehouse inventory management, tracking the right KPIs is crucial. Here are some key metrics to keep an eye on:
-
Inventory accuracy rates: This measures how closely the recorded inventory matches the actual inventory. The industry benchmark is 99.3% according to the WERC DC Measures Report. A high accuracy rate means fewer errors and happier customers.
-
Order fulfillment accuracy: This shows how often orders are filled correctly. A good target is 99 %+, as highlighted by NetSuite. If your accuracy is high, customers are more likely to come back.
-
Inventory turnover rate: This metric tells you how often your inventory is sold and replaced over a period. A higher turnover rate indicates good sales and efficient inventory management.
-
Carrying/holding costs: These are the costs of storing unsold goods. Automating inventory management can reduce these costs by up to 20%, according to Infor. Lower cost means more profit.
-
Stockout and overstock frequency: Knowing how often you run out of stock (stockouts) or have too much (overstock) helps maintain balance. According to the US Department of Commerce, managing these can save money and improve service.
-
Cycle time for order processing: This is the time it takes from receiving an order to shipping it out. Shorter times mean faster service and happier customers.
-
Labor productivity: This measures how efficiently your staff works. Higher productivity means more work done in less time, which can lead to lower costs and better service.
Tracking these KPIs can give you insights into your warehouse operations. They can help you find areas for improvement and boost overall efficiency
Common Challenges and How to Overcome Them
Managing warehouse inventory isn’t always smooth sailing. Here are some common challenges and ways to tackle them:
Stockouts, Overstocking, and Lost Inventory
Stockouts can frustrate customers. Imagine running out of a popular item. It leads to missed sales. On the flip side, overstocking ties up cash. Both hurt your bottom line. Lost inventory? It’s like throwing money away. To fix this:
- Track inventory levels closely.
- Use accurate forecasting methods.
- Implement just-in-time inventory systems.
Data Inaccuracies and Their Root Causes
Data inaccuracies can cause chaos. Wrong numbers lead to poor decisions. Why does this happen?
- Manual entry mistakes.
- Lack of real-time updates.
- Poorly integrated systems.
To overcome this:
- Invest in reliable software.
- Regularly audit your data.
- Train staff on data entry best practices.
Labor Inefficiencies and Training Gaps
Labor inefficiencies slow down operations. Untrained staff can struggle with tasks. This leads to delays and errors. To improve:
- Provide regular training sessions.
- Create clear processes.
- Encourage open communication among staff.
Technology Adoption Barriers
Not everyone is tech-savvy. Some may resist new tools. This can hold back your operations. To ease the transition:
- Offer hands-on training for new systems.
- Share success stories from early adopters.
- Highlight the benefits of technology.
Solutions
Here are some solutions that can help:
- Automation: Streamline repetitive tasks.
- System Integration: Connect different software to ensure smooth data flow.
- Staff Training: Keep everyone updated on best practices.
- Continuous Process Improvement: Regularly assess and refine processes.
By addressing these challenges, you can create a more efficient warehouse inventory management system.
Selecting the Right Inventory Management System
Choosing the right inventory management system is crucial. It can make or break your operations. Here’s what to consider:
Assessing Business Needs and Warehouse Size
Not all businesses are the same. Start by understanding your specific needs. Ask yourself:
- What type of products do you handle?
- How much inventory do you manage?
- What are your growth plans?
Your warehouse size matters too. A small warehouse may need a simpler system. A larger one will require something more robust.
Key Features to Look For
Look for systems that offer:
- Real-time tracking: You want to know where your items are at any moment.
- Integration: Can it connect with your existing software? This saves time.
- Scalability: Will it grow with your business? You don’t want to outgrow your system too soon.
Evaluating Software Providers
Research potential providers. Check their reputation. Read reviews and testimonials. Ask for demos. Make sure the software fits your needs before committing.
Calculating ROI and Implementation Costs
Consider the costs involved. Look at:
- Initial purchase price
- Ongoing fees
- Training costs
Calculate your return on investment. Will the system save you time and money? If yes, it’s worth considering.
Future-proofing: Cloud, Mobile, and Automation Readiness
Think about the future. Choose a system that:
- Is cloud-based: This allows access from anywhere.
- Has mobile capabilities: It helps manage inventory on the go.
- Supports automation: This can streamline tasks and reduce errors.
In summary, selecting the right inventory management system is about understanding your needs, evaluating features, and planning for the future.
Future Trends in Warehouse Inventory Management
The warehouse inventory management landscape is changing fast. Here are some key trends shaping the future:
-
Growth of the WMS Market: The warehouse management system (WMS) market is booming. According to Grand View Research, it’s expected to grow significantly in the coming years. More companies are investing in these systems to streamline operations.
-
Real-Time and Predictive Analytics: Businesses want faster insights. Real-time data helps in decision-making. Predictive analytics can forecast inventory needs. This means fewer stockouts and overstock situations. It’s like having a crystal ball for inventory.
-
AI, Robotics, and IoT: Technology is taking center stage. Artificial intelligence is improving efficiency. Robotics helps with picking and packing. The Internet of Things (IoT) connects devices for better tracking. Together, these technologies make warehouses smarter and more efficient.
-
Sustainability Initiatives: There’s a growing push for green warehousing. Companies are focusing on sustainable practices, including reducing waste and energy use. This is not just good for the planet; it can also cut costs.
These trends point to a future where warehouse inventory management is more efficient and eco-friendly.
Conclusion
Effective Warehouse Inventory Management (WIM) is essential for the success of any business that deals with physical products. It enables companies to accurately track their inventory, ensuring that items are properly stored, organized, and readily available when needed. As a result, businesses can deliver the right products to the right place at the right time—leading to smoother operations and higher customer satisfaction.
But the work doesn’t stop here. Businesses must adapt and improve their WIM practices regularly. The market changes. Customer needs shift. New technologies emerge. To stay ahead, companies should:
- Continuously evaluate their inventory processes
- Invest in new tools and technologies
- Train staff on best practices
In summary, a strong WIM system is not just about keeping track of stock. It’s about thriving in a competitive landscape. Adaptation and improvement are key to long-term success.
FAQ
What are the main benefits of using warehouse inventory management systems?
Warehouse inventory management systems help reduce labor costs. They improve inventory accuracy. They speed up order fulfillment. Plus, they minimize stockouts and overstocking. This boosts profitability and customer satisfaction. (NetSuite, Infor)
How can businesses achieve high inventory accuracy in their warehouses?
Businesses can achieve high inventory accuracy by:
- Implementing advanced inventory management software
- Utilizing barcoding or RFID
- Conducting regular audits
- Training staff
With these steps, the industry average for inventory accuracy is now 99.3%. (WERC DC Measures Report)
What are the biggest challenges in warehouse inventory management, and how are they addressed?
The biggest challenges include:
- Stockouts
- Overstocking
- Inaccurate data
- Inefficient processes
These challenges are addressed through automation. Regular audits help too. Staff training and ongoing process optimization are also key. (US Department of Commerce, Infor)
Connect with Cubework
Join thousands of businesses thriving in our spaces! From startups to enterprise-level operations, Cubework provides premium commercial solutions. Find your ideal space now! Call us at 888-599-7809 or email us at info@cubework.com.